Continuous Upskilling : Need of the Hour
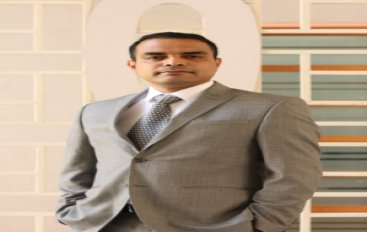
With automation and compliance to technologies supporting enhancement of Industry 4.0 rigorously, there is an enormous elephant in the room that needs to be addressed for a smooth transition into digitalization- will human jobs be replaced by machines. Despite no single answer to the debate, the most probable scenario remains with some jobs becoming redundant, as automation can complete the work with increased efficiency and accuracy. One such example is the banking industry where payments and accounts have moved online, thereby minimalizing human interaction. This fear of jobs being taken over by automation, could turn into a reality for most industries today, if they don’t embrace the ongoing digital revolution and bolster their skills to match up to market needs.
Upskilling has long evolved from being just a choice. Today, it is a necessity for the incoming generation of employees as well as those, who would like to continue working. As the pace of digitization would not pause, it is imperative that there is a continued, uninterrupted and rapid upskilling done for the employees in a company for it to survive as well. New talent, with expertise in newer digital technologies need to be added to their payrolls while existing ones are scaled up to be retained. The company structures also need to evolve to help their employees learn new skills and meet their dreams in an organization.
The grimness of the situation for those avoiding upskilling was evident in the NASSCOM President R Chandrashekhar said in May, "There needs to be continued re-skilling, or either be prepared to perish. This is the new mantra." A report in the same month denied panic in the IT industry regarding layoffs and large-scale job losses but instead said that the sector has been embracing the nearly 6 lakh new jobs that have been added over the last three years, including the 1.7 lakh jobs created in 2016-17. The report further said that in the IT sector, up to 40% professionals of the estimated four million workforce need to be upskilled within the next five years, if they need to match up to the dynamism and automation in industry.
And companies, today, are paying heed to these figures. They are increasingly modifying their talent acquisition and retention policies to focus on agility based hiring rather than going for competency solely. With the advent of high-end technologies, processes are being rehashed and customized as per specific needs, and in this ecosystem, the need of the hour is for employees to be on their marks to learn, unlearn and relearn new techniques in a meticulous and rapid fashion.
The requirement works in tandem with HR policies and operational processes becoming more real-time and dynamic with connected devices. While newer technologies and machines work to standardize perfection and customization for their products, employees are now needed to familiarize themselves with the workings of these machines and codes to use them efficiently. This needs a significant transformation in the way that employees approach a product and the process used to make it- from design to manufacturing. One such industry that is embracing the change is the automotive sector.
With the BS-VI norms almost ready to be implemented for the sector, companies are ramping up the process of adaptation of newer technologies to revolutionize their designs that leverage hybrid and electric cars to cut emissions. In the process, the sector is now looking to leverage unique and tailor-made technologies that make the vehicles appealing to the customer to move beyond just an assembly line focussed on mass production. To make use of the new approach, the workforce in the industry is unlearning older methods to relearn design and manufacturing that can tailor-make vehicles for the newer customers. Techniques like data collation and monitoring, analytics and shop floor integration need to be collated and analysed to increase productivity and efficiency and the workforce need to upskill themselves to match industry demands. They need to understand the filter out the terabytes of data streaming in from various connected devices, analyse them to gather insights and finally leverage them to increase their understanding of the market and customers, predict upcoming trends and consistently create a differentiated product. Companies must leverage the utilities of the ongoing shop floor integration to streamline processes and cut their costs and time to increase the organization’s productivity and profitability.
To capitalize on the incoming technologies with Industry 4.0, companies need to help their employees understand and use the high-end technologies and machinery. Companies need to hire and retain those who can bring that agility to unlearn and relearn rapidly and use these traits to evaluate the employees. Organizations need to implement and follow a three-pronged model of evaluating employees based on performance, learning and business and create processes to interlink them and make them interdependent. We need to figure out a way to translate these behaviours into traits that are measurable in nature. We also need to have an assessment methodology in place to evaluate these traits objectively.
The IT industry is also transforming processes and is now rapidly scaling up existing technologies to work in tandem with the ongoing digital revolution to transition into a digital entity smoothly. This evolution is creating new jobs with expertise in software and hardware innovations by redesigning and rethinking and rehashing their manufacturing processes. The sector is embedding digitalization and perfecting the skills in the sector to bring a global spotlight to the Indian IT sector through differentiating innovations. This derives the need for the workforce to change their thought processes too, to imbibe innovation at the core of their work. Meanwhile, companies need to step in to empower their mass workforce to experiment more to create innovations that would be in line with a company’s aim of becoming a pioneer in their field with a differentiated product.
Organizations are increasing their investment into research and development to reach the scale that they envision themselves in the digital future. They need to develop methodologies and programs that help individual employees to explore their skills better and independently, to keep the creativity to stay ahead of the competition, alive. It is to embrace this change that feedback and review cycles have advanced from yearly to a quarterly basis in several companies. Today, collating feedback is real-time, while the team structures are becoming more dynamic and project-specific to avoid perishing in the dynamism of the industry.
A case in point is the coal industry, which was once a poster boy for innovation. Today, however, the industry is facing the brunt of adopting more renewable sources of energy that have zero emissions. The sector is facing a decline in sales and several have misconstrued it as a loss in the number of jobs. However, once a person looks closer, it is evident that there are different demands in the sector, which is now leaning towards hybrid sources of energy, which are still affordable for a nation-wide use. There are jobs for handling digital hardware, collating and analysing data, technical expertise, software upgradation of machines etc. Companies stand at the precipice of upskilling their employees to embolden their expertise in hybrid and renewable energies or stand to watch the industry become obsolete.
This conundrum of automation or jobs has also received an indirect answer from the government which has created several federal programs to upskill people to increase employment. One such example that the government runs is the Garib Nawaz program that aims to offer employment oriented training to youth from minority communities. While the government triggers a socio-economic change with these programs, companies have also stepped up their game in terms of programs to help employees catch up with the changing demands in the market and pave way for a seamless transition into Industry 4.0. By getting the workforce ready to unlock new methods of efficient production and delivery, the results would not only lead to a socio-economic change in a country but would also allow a company to stay ahead of the market through unique innovations by their upskilled employees.